Unlocking Data on the Plant Floor: Why It’s Still So Hard and Why It Matters
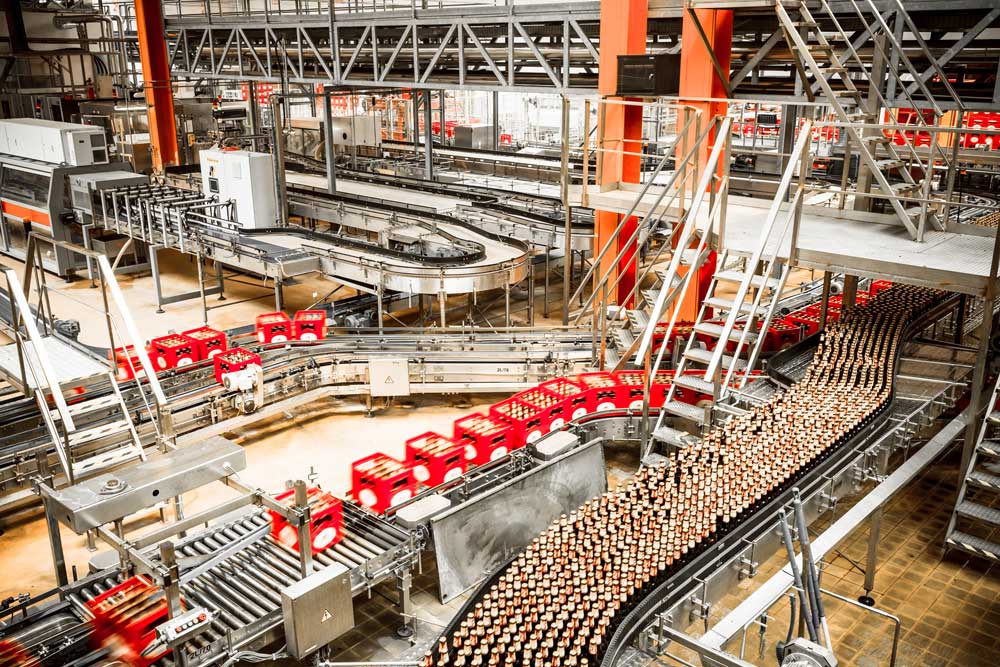
In a world full of smart sensors, cloud platforms, and real-time dashboards, it seems like capturing operational data from the manufacturing floor should be easy. But for many ag manufacturers, it’s still one of the toughest challenges they face.
Why? Because too often, the numbers we rely on, cost of goods sold, productivity rates, labor efficiency, are built on estimates, not actual data. And when that happens, decisions become educated guesses instead of informed moves.
Let’s unpack what’s standing in the way:
1. Outdated Systems with No Easy Data Path
Much of the equipment still in use was never designed to share its data beyond a local display or printed report. These machines might still run well, but the data they generate stays locked inside, isolated and inaccessible to modern analytics tools.
And even when data is collected, some ERP systems are “closed boxes” that don’t play well with other tools. That means you can’t generate the reports you actually need, when you need them.
2. Digitally Disconnected Operations
Many plants are deliberately isolated from the rest of the network, often for cybersecurity reasons or because legacy systems can’t be updated. While this protects the plant, it also disconnects it, creating data silos where visibility is lost and responsiveness suffers.
3. Labor Tracking Lags Behind
Tying labor data to specific lines or jobs is notoriously tricky. Most systems track labor in the aggregate, but this doesn’t help you understand where your workforce is making the biggest impact or where time and money are slipping through the cracks.
In an industry where margins are tight, you can’t afford to run without precision. Without detailed data, fine-tuning performance becomes almost impossible.
This Isn’t Just a Technical Problem, It’s a Strategic One
Too many organizations treat plant data as a “nice-to-have,” not a must-have. But operational data should be considered as fundamental as water, electricity, or labor.
Until data is valued and invested in at that level, it will remain underutilized—and so will your team’s potential.
The Good News? This Can Change
By investing in secure, connected systems and building a process to tie labor, production, and cost together, manufacturers can gain true performance insight. This kind of clarity builds confidence, fuels smarter decisions, and makes continuous improvement a reality. And when you can trust the data, you can trust the decisions.
Contact ZAG to learn more.